The quenching process in forging swords
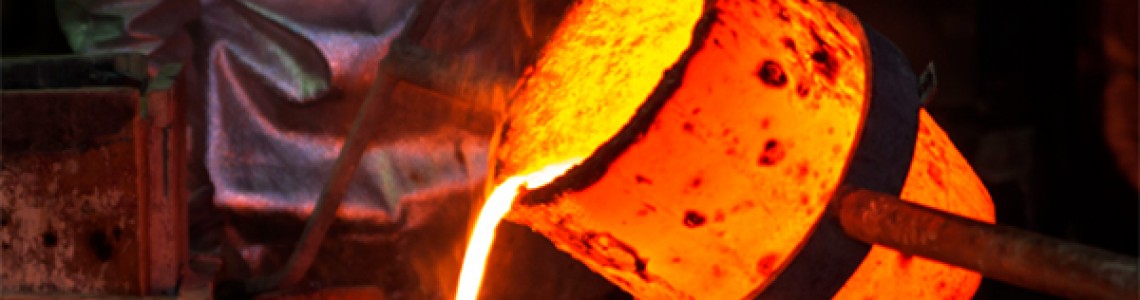
Heat treatment is one of the important processes in the manufacture of swords, Whether it is a Japanese sword or a Chinese sword, and it is the soul of the performance of the sword. Heat treatment does not change the shape of the sword itself and the overall chemical composition, but by changing the internal microstructure, or changing the chemical composition of the surface, to give or improve the performance. And this is generally not visible to the naked eye. But it has a greater impact on the quality of swords, and the level of a swordsmith can also be seen from the heat treatment process.
Heat treatment is a process in which metal (steel) is heated to a suitable temperature in a certain medium, and then kept at this temperature for a certain period of time, and then cooled at different speeds.
In the process of making tools, I think the quenching process is the most complicated and difficult to control. The reason why the quenching process is complicated is that in order to obtain martensite during quenching, the cooling rate must be greater than the critical cooling rate, and rapid cooling inevitably causes greater internal stress, which often causes deformation or cracking of the blade, or makes the sword tough Lower, the cutting edge is easy to crack during use. If the cooling rate is less than the critical rate, the horse body will not be obtained after quenching, and the hardness, wear resistance and sharpness of the blade will be insufficient. Therefore, during quenching, the cooling rate must be just right, not only to ensure that martensite is obtained, but also to reduce deformation, prevent cracking, and maintain toughness. This is the most important problem in the quenching process.
Quenching: After the workpiece is heated and kept warm, it is quickly cooled in quenching medium such as water, oil, other inorganic salts, and organic aqueous solutions. After quenching, the steel becomes hard, but at the same time it becomes brittle. In order to reduce the brittleness of steel parts, the quenched steel parts are kept at an appropriate temperature higher than room temperature and lower than 710°C for a long time, and then cooled. This process is called tempering. Annealing, normalizing, quenching, and tempering are the "four fires" in the overall heat treatment. Quenching and tempering are closely related and are often used in conjunction with each other. After "strong forging", a special quenching agent is used for "softening" treatment to make the blade rigid and flexible, capable of bending and stretching. It belongs to high-precision craftsmanship, which is not handy for ordinary craftsmen.
1. The most ideal cooling rate during quenching
In order to meet the above requirements, we must first grasp the ideal cooling rate when steel is quenched. From the coordinate graph of the isothermal transformation curve of supercooled austenite above, we can know that the transformation speed of supercooled austenite in the range of 650-500 degrees is the fastest. Above this temperature range and below this temperature range, The undercooled austenite is relatively stable, and the transformation speed is slightly slower. Therefore, to obtain martensite during quenching, it does not need to be cooled rapidly during the entire cooling process, but rapidly cooled between 650 and 500 degrees. Above 650 degrees, the cooling can be slower to reduce the temperature difference between the inside and outside of the cutter. The thermal stress can be cooled down a bit more slowly below 300 degrees to avoid the sequential transformation of austenite to martensite, causing excessive structural stress (below 300 degrees, the plasticity of the steel is small, the strength is large, and the thermal stress It can easily cause deformation and cracking in conjunction with tissue stress). In summary, the ideal quenching cooling rate of steel is: from slow (above 650 degrees) to fast (650-500 degrees) and then to slow (below 300 degrees) cooling process.
2, select the appropriate quenching agent and quenching method
Analyze the cooling capacity of various commonly used quenching agents and their respective limitations, select the appropriate quenching agent and quenching method, so that the actual cooling rate of the steel during quenching is close to the ideal cooling rate.
1) The cooling capacity of water at 650-500 degrees is very large and it is easy to harden, but the cooling rate is still too fast at 300-150 degrees, and a large amount of internal stress will remain, which will make the toughness of the cutter body insufficient and quench cracks in severe cases.
2) The cooling capacity of oil in the range of 300-200 degrees is small, and it is not easy to be quenched, but the cooling capacity is not large at 650-500 degrees, which is not as good as the cooling capacity of water, and it is not easy to harden.
3) Use water and oil double liquid quenching method to make the actual cooling rate close to the ideal cooling rate. The sword heated to austenitization is first quenched into water, and it is estimated to be quickly transferred to oil when it is cooled to 400-300 degrees, so that the supercooled austenite is slowly transformed into martensite in the oil. In this way, high hardness martensite can be ensured while maintaining good toughness, reducing internal stress and preventing deformation and cracking, which is an ideal quenching method. The key is to master the time spent in the water. My general experience is less than 1.5 seconds, usually 1 second. When the thickness of the blade is large, increase the water residence time appropriately, but not more than 1.5 seconds. If you are not experienced enough, you can first take a few leftovers as samples and practice several times, and remember the best time after checking the hardness.
4), the quenching method using clay tempered
3. Measures to prevent cracking
From the above analysis, it can be seen that the reason for blade quenching is not due to shrinkage when the blade cools and shrinks, but because the tensile stress generated by the blade bending backwards when the blade cools and shrinks to tear the blade. Generally, the crack is mainly in the blade. Where there is a curved turn, the stress is most concentrated here. The measure to avoid cracking is to use the residual temperature of the blade back to temper the blade in time. My general approach is: For single-edged knives, you don't need to burn the blade with soil, so that you can judge the temperature by color. Dip the reddish blade into the water, with the blade down, the depth of immersion is half of the width of the blade, a bit inclined, and the tip of the blade should just be immersed in the water. Keep it for 1 to 1.5 seconds (the blade has cooled to 200 degrees at this time) Below, and the back of the blade is still in red), quickly lift the blade from the water and keep your eyes on the boundary between the cold and hot areas of the blade. At this time, a "rainbow" will appear between the boundary lines. Under the effect of the remaining temperature on the back of the sword, the "rainbow" moves towards the blade. When the golden area of the "rainbow" is close to the edge of the blade, the blade is immersed in the water again, and quickly lifted up again, still closely watching the changes of the "rainbow", As the "Rainbow" continued to move towards the blade, the blade was immersed in the water again. In short, after the burning of the blade, it is best that the "rainbow" golden area just enters the edge of the blade! The actual operation process must be fast and fast. If the tempering is not timely, the blade may be quenched. Even if it does not crack, the blade has insufficient toughness and is easy to collapse. Mouth; the tempering temperature is too high and the quenching is not hard. Unfamiliar sword friends can try with a few iron plates at first, and then try the sword after seeing clearly, so as to avoid unnecessary losses. The bearing steel processed by this method can be chopped vigorously without crimping or chipping (thick edge). The effect is very satisfactory.
4, the final description
1) The above method is suitable for single-edged swords that are not too long, and double-edged swords will not be discussed temporarily.
2). Different steels have different tempering temperatures. For example, the golden area of "rainbow" for bearing steel is the best to reach the cutting edge, while the spring steel can be blue close to the cutting edge. Regarding the tempering color scale temperature, I have the opportunity to repeat it later.
3), you can click here to browse and customize your own suitable sword.
Want a unique sword? Feel free to contact us:
Phone: 086 13739276006
Email: [email protected]
Website: www.hanbonforge.com
Custom Sword Page: www.hanbonforge.com/CUSTOM-SWORDS/Custom-Your-Own-Swords
Leave a Comment