How is the bronze sword made?
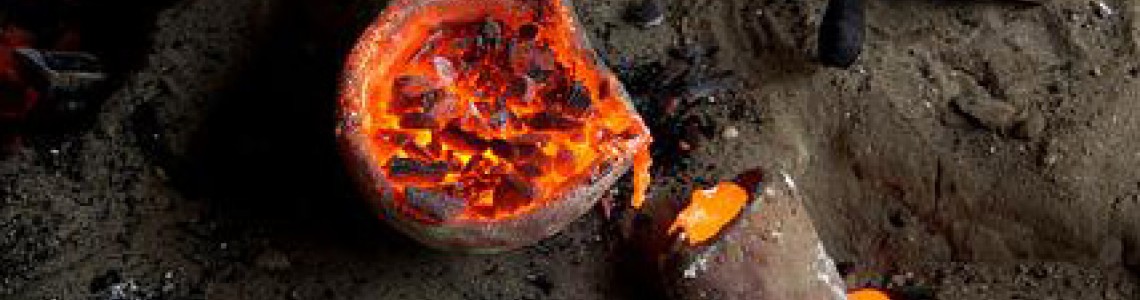
As we all know, Japanese samurai swords are currently popular swords, and most of them are made of high-carbon steel, but before the invention of high-carbon steel, iron was used to make swords. Before iron was invented, bronze was used for this purpose. Except for the subtle differences in strength and ductility, the manufacturing process of bronze swords is different from that of iron swords. Many centuries ago, professional swordsmiths made bronze swords by casting molten bronze into the shape of a sword, and then they would sharpen and polish the blade. Among the Wuyue bronze swords, the most eye-catching ones are the Wuwangjian and the Yuewangjian.
Casting overview
The fundamental difference between making iron swords and making copper swords is that the former is forged while the latter is cast. In order to make a bronze sword, the swordsmith will smelt the bronze until it becomes hot liquid metal, and then he puts it in a cavity formed by the shape of a sword. Once the bronze metal has cooled, the swordsmith will take it out to complete the sword making process.
Casting has existed much longer than forging. According to "Metal Casting: Computer Aided Design and Analysis", the process is about 6,000 years old, and some of the earliest examples of cast metal can be traced back to around 3,200 BC.
Trim
Another important step in the process of casting a bronze sword is trimming. Trimming refers to cutting, grinding, sanding and removing unwanted metal fragments. When casting a sword, defects will occur in the mold. Some of these defects are subtle and consist of small metal shavings embedded in the blade, while others are larger and more important. Either way, the swordsmith must remove these defects through a process called trimming.
In most cases, the swordsmith gave this task to another professional, the repairer. The monk is responsible for removing blemishes on cast swords, usually by using cutting, grinding and sanding blades. However, this is hard work, and it is not without cost. Fettlers often suffer from health problems due to exposure to metal shavings.
Casting and forging
For thousands of years, casting and forging have been used to make swords, but it is undeniable that forging is a better method. Through forging, the swordsmith can better control this process. For example, in feudal Japan, swordsmen would cool the spine and blade of a sword at different speeds to achieve a flexible spine and a hard blade. Known as differential heat treatment, it has become a basic feature of high-quality Japanese swords. Unfortunately, due to the way the metal is smelted and poured into the cavity, casting does not allow for differential heat treatment.
Forging also allows for sharper and stronger blades. This was a key factor in the period of feudal Japan, because samurai needed sharp swords like katana and wakizashi to defend against Mongolian invaders.
As you can see, the manufacturing process of bronze swords is different from steel swords because they are cast instead of forged.
Discover the many attractive options available for Katana swords and custom swords.
Want a unique sword? Feel free to contact us:
Phone: 086 13739276006
Email: [email protected]
Website: www.hanbonforge.com
Custom Sword Page: www.hanbonforge.com/CUSTOM-SWORDS/Custom-Your-Own-Swords
Leave a Comment